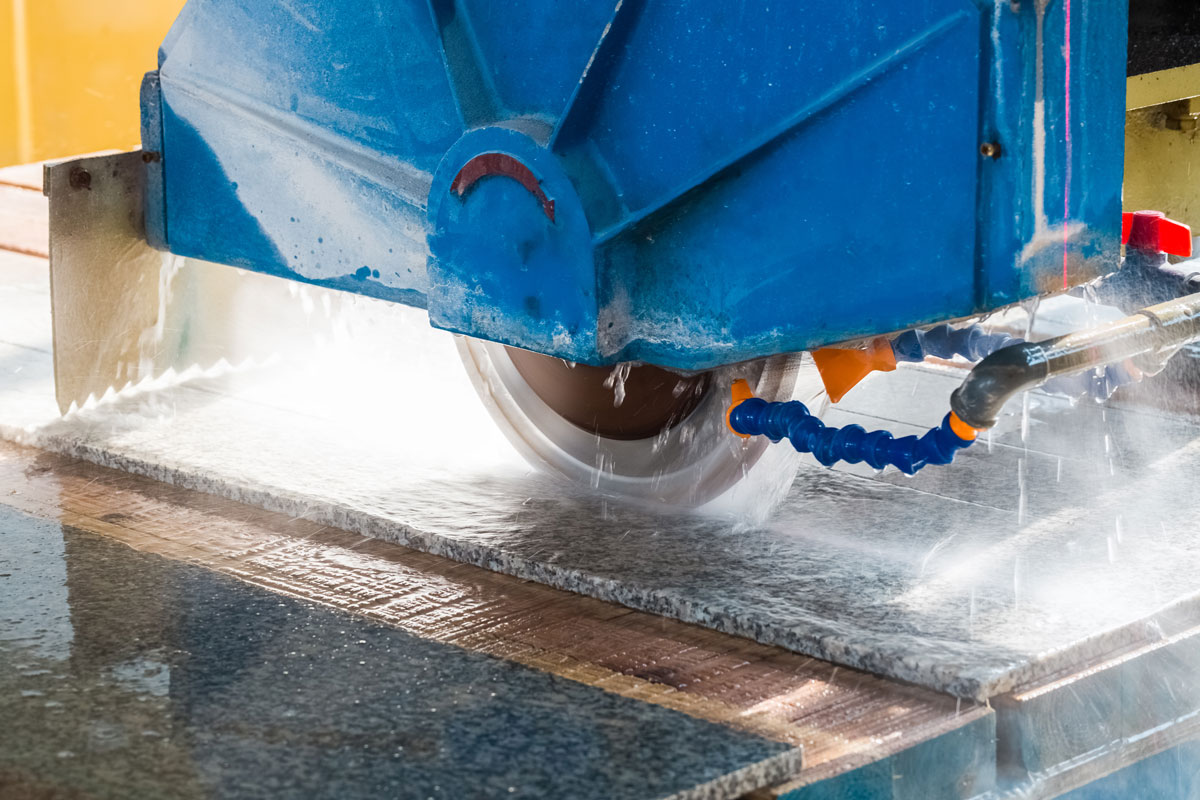
Fabrication
The sequence of events which brings natural stone from the quarry to the home has not changed much since stone entered the homes of the ancient Greeks. Large blocks of stone are cut from the quarry. From those blocks, thin pieces of stone are cut called slabs. The slabs are then shaped and polished and shipped for installation. What has changed dramatically over the years is the type of machinery used in this age-old sequence. Three basic types of machines are involved in the fabrication process: saws, polishers, and routers. Saws perform several functions during fabrication. A block saw, or gang saw, cuts the massive stone blocks into slabs. These days, diamond wire saws make short work of this task. A metal wire is studded with industrial-grade or synthetic diamonds, and this wire quickly cuts through stone as hard as granite. A bridge saw is then used to cut the stone slab into the proper shape for its application, whether it be a countertop or a sink. These saws typically use circular metal blades studded with diamonds, and water is sprayed onto the blade to cool it during the cutting process. Modern technology has produced a new type of saw utilizing water jets combined with an abrasive material, which cuts edges and holes quickly and smoothly, and many fabricators are upgrading to these machines.
Polishers grind down the naturally rough surface of the stone to whatever finish the consumer desires. Hard stones like marble and granite can be polished all the way to a mirror finish. The polisher consists of rotating pads which are surfaced with an abrasive substance. The finer and smaller the abrasive grits are, the higher the polish. Most modern polishers can produce a variety of finishes, from the smooth, soft look of a honed finish to a slick, shiny mirror finish…even decorative finishes like flamed, tumbled, or hammered. Routers create edge profiles on a slab, and cut designs on larger pieces like fireplace mantles and hearths. There are dozens of standard edges for countertops and tables, from simple to highly decorative. Routers have a spinning blade covered with diamonds which is water-cooled. It travels along the edge of the slab to shape it. In the past, these machines were either operated by hand, or had some limited automatic function. The time needed to create a finished countertop was significant. A countertop with a complex edge profile might take three weeks or longer.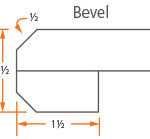


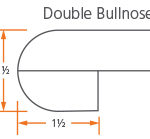
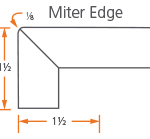
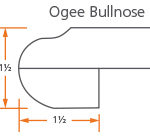
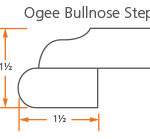

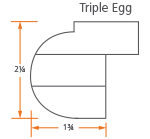

Choosing Edge Detail
We will work with you to select the most suitable edge detail to fit your project, your individual ideas, suggesting from our design experience with our edge detail selection. We will work with you to select & achieve the look you desire.
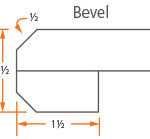


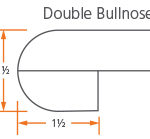
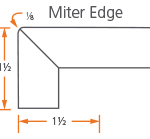
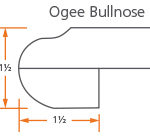
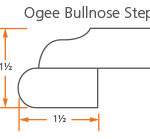

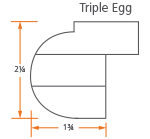
The Process
- Grind, sand, clean, or polish objects or parts to correct defects or to prepare surfaces for further finishing, using hand tools and power tools.
- Move controls to adjust, start, or stop equipment during grinding and polishing processes.
- Remove completed workpieces from equipment or work tables, using hand tools, and place workpieces in containers.
- Load and adjust workpieces onto equipment or work tables, using hand tools.
- Measure and mark equipment, objects, or parts to ensure grinding and polishing standards are met.
- Trim, scrape, or deburr objects or parts, using chisels, scrapers, and other hand tools and equipment.
- Verify quality of finished workpieces by inspecting them, comparing them to templates, measuring their dimensions, or testing them in working machinery.
- Select files or other abrasives, according to materials, sizes and shapes of workpieces, amount of stock to be removed, finishes specified, and steps in finishing processes.
- Transfer equipment, objects, or parts to specified work areas, using moving devices.
- Record product and processing data on specified forms.
- Mark defects such as knotholes, cracks, and splits for repair.
- Spread emery powder or other polishing compounds on stone, or wet stone surfaces using hoses, then guide buffing wheels over stone to polish surfaces.
- Apply solutions and chemicals to equipment, objects, or parts, using hand tools.
- Repair and maintain equipment, objects, or parts, using hand tools.
- File grooved, contoured, and irregular surfaces of metal objects, such as metalworking dies and machine parts, to conform to templates, other parts, layouts, or blueprint specifications.
- Study blueprints or layouts to determine how to lay out workpieces or saw out templates.
- Sharpen abrasive grinding tools, using machines and hand tools.
- Wash grit from stone, using hoses.
- Clean brass particles from files by drawing file cards through file grooves.
- Fill cracks or imperfections in marble with wax that matches the stone color.